Radio shuttle racking offers warehouses a high-density, efficient, and safe storage solution that can improve overall productivity and reduce operational costs. By automating the movement of pallets within storage lanes, this system enhances inventory management, maximizes space, and provides flexibility for growing businesses. For warehouses dealing with high turnover or seasonal products, the advantages of radio shuttle racking make it a strategic investment that can streamline operations and improve profitability.
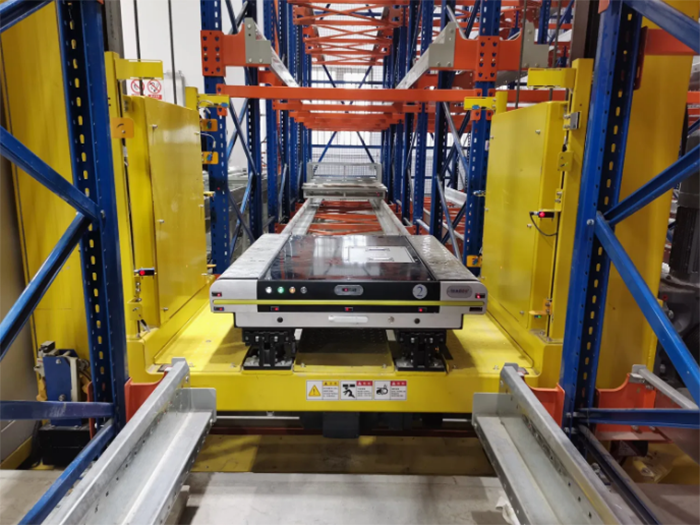
1. Maximized Storage Space
High-Density Storage: Radio shuttle racking maximizes storage density by reducing the number of aisles required, making it ideal for warehouses with limited space.
Efficient Use of Vertical Space: Pallets can be stacked higher, allowing for better utilization of the warehouse’s vertical capacity.
2. Increased Operational Efficiency
Faster Loading and Unloading: The radio shuttle moves pallets swiftly within the racking, reducing handling time and speeding up loading and unloading operations.
Reduced Forklift Travel Time: Since forklifts only need to place pallets at the entry point, their travel distance is minimized, allowing operators to focus on other tasks.
3. Enhanced Safety
Minimized Forklift Maneuvering: By eliminating the need for forklifts to enter the racking structure, the risk of collisions and rack damage is significantly reduced.
Improved Worker Safety: Workers are less exposed to potential accidents caused by forklift traffic within the storage lanes.
4. Versatile Storage Options
FIFO and LIFO Capabilities: Radio shuttle racking can support both FIFO (First-In, First-Out) and LIFO (Last-In, First-Out) inventory management methods, making it adaptable to various storage needs.
Storage for Various Goods: The system can handle different types of goods, including pallets of varying sizes and weights.
5. Cost Savings
Lower Operational Costs: Reduced labor and forklift usage lead to cost savings over time. The faster operations also improve overall productivity.
Reduced Maintenance Costs: With fewer forklift interactions, the wear and tear on racking structures are minimized, decreasing maintenance expenses.
6. Improved Inventory Management
Accurate Tracking: Some advanced radio shuttle systems are equipped with sensors to track inventory, enhancing stock visibility and accuracy.
Minimized Product Damage: Automated pallet handling reduces the risk of product damage compared to manual handling.
7. Energy Efficiency
Battery-Powered Shuttles: The shuttles are typically powered by rechargeable batteries, making them an energy-efficient solution that reduces fuel consumption compared to traditional forklift operations.
Eco-Friendly Operations: Less forklift usage means lower carbon emissions, contributing to a more sustainable warehouse environment.
8. Flexibility and Scalability
Expandable System: The system can be easily expanded as storage needs grow, allowing warehouses to scale their operations without significant structural changes.
Flexible Configuration: Racking configurations can be adjusted to accommodate different pallet types and warehouse layouts.