The importance of a well-organized warehouse is crucial to ensure that a company's logistics processes are as productive, efficient and flexible as possible. It is not straightforward to improve the performance of a warehouse or distribution center, as it requires sound ongoing planning and depends on many elements overall, not just the storage system.
Proper planning of each warehouse affords companies extraordinary benefits, such as full utilization of space, time savings in all processes, and reduced and optimized costs, resulting in greater profitability and good inventory organization.
Unfortunately, it is not always possible to achieve good warehouse management. The following is a list of typical annotation errors that prevent proper warehouse organization
Low awareness of product location
This problem occurs when warehouses are not well organized and when warehouse personnel do not know where products are located due to lack of knowledge or incorrectly marking products with their identification codes. This delays the entire process including customer delivery times.
Poor warehouse design leads to lack of space
Problems occur when inventory or stock storage is poor, when each product is not stored in its location, and when aisles are not respected and everything is placed in the corner. This is usually due to incorrect planning and design of the warehouse layout at the time of creation.
Inventory problems
Sometimes warehouses suffer from out-of-stocks because they fail to always have the highly requested products. It is critical to secure the customer's goods to ensure their satisfaction and delivery time.
Poor human resource management
Sometimes warehouse workers are unable to execute processes correctly simply because they are poorly organized, unfamiliar with their activities or overworked.
How to avoid common warehouse management mistakes?
Regular on-site inspections
You should make a plan to regularly review the layout of your warehouse and check the composition of your warehouse inventory. This is because improving the warehouse layout also requires reallocation based on product mix. Please ensure that you do this at least once a year.
Make sure you pay special attention to the dimensions of your shelves in order to make the most of the entire height, length and width of the space. To do this, it is highly recommended that you run a report of all goods handled for at least one year and group them by dimension.
This will give you a clear picture of the required rack configuration and storage allocation settings. It is likely that you are facing a poor optimization of warehouse space rather than a shortage of space.
If measuring the dimensions of your goods is causing or will cause additional overhead, you can automate this process by implementing a volume measurement system for pallets and parcels.
Using modern logistics management equipment
Common logistics management equipment such as warehouse management systems, wearable computers, business intelligence dashboards, splitters and conveyors, barcode scanners, mobile printers and volumetric systems can all be used in combination to help you digitize your warehouse, increase efficiency and automate your warehouse operations.
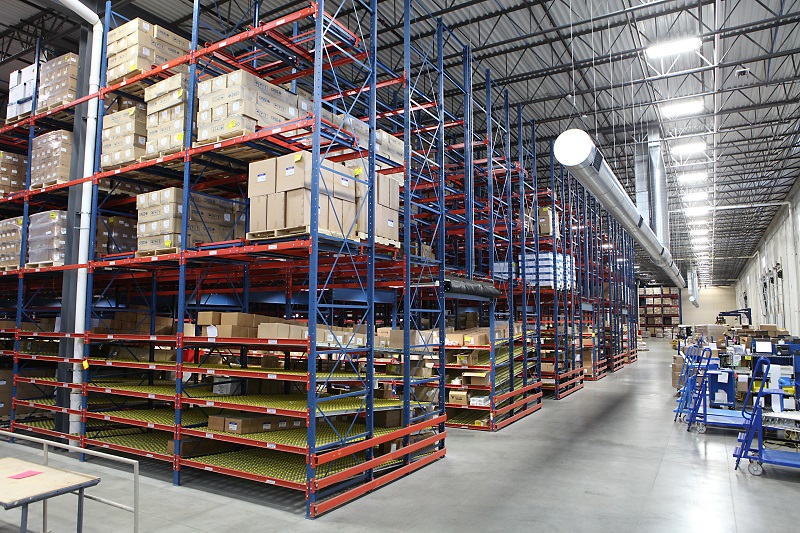
Further Reading:
Introduction to the benefits of mezzanine floors
Reasons for storing lumber on cantilevered racks
Six Cost-Effective and Secure Warehouse Storage Solutions
Six Creative Ways to Use Cantilever Racking
Introduction of three common types of industrial racks